La histórica planta de Toyota en Georgetown, Kentucky, se transforma en referente global gracias al proyecto “K-flex”, que promete fabricar cualquier modelo bajo demanda en una misma línea.
En el corazón de Kentucky, la planta de Toyota —la primera del fabricante japonés en suelo estadounidense— está más cerca que nunca de cumplir un viejo sueño de la industria automotriz: producir cualquier vehículo, en cualquier momento y sobre una misma línea de ensamblaje. Y no se trata de una promesa futura, sino de una realidad que empieza a materializarse gracias a un ambicioso proyecto de más de 1.800 millones de dólares llamado internamente “K-flex”.
La transformación se ha concentrado en la emblemática Línea 1 de Georgetown, que tras cuatro décadas produciendo Camrys, emerge ahora como posiblemente la línea de ensamblaje más flexible del mundo. Gracias a este rediseño, la planta será capaz de fabricar vehículos híbridos, de combustión, enchufables e incluso eléctricos puros, siempre que estén construidos sobre la plataforma global TNGA-K de Toyota. Entre ellos: Camry, RAV4, Highlander, Sienna, y nuevos modelos eléctricos aún por anunciar.
“Queríamos fabricar cualquiera de ellos, sin importar su tren motriz”, explica Stephen Brennan, vicepresidente senior de operaciones de manufactura de Toyota y creador del proyecto. “Así que tomamos nuestro vehículo más grande y adaptamos todo el sistema para que no requiera modificaciones futuras”.
Chasis diagonal, robots autónomos y cero cintas magnéticas
Una de las principales innovaciones es la posición diagonal del chasis durante el ensamblaje, una rareza en la industria. En lugar de moverse de frente o de cola, los vehículos se desplazan de costado, lo que facilita el trabajo de los operarios bajo el auto y mejora las condiciones para la automatización.
La automatización juega un papel central en esta nueva línea. Pequeños robots OTTO se encargan de mover estanterías completas con piezas hacia las estaciones necesarias, mientras que plataformas planas del tamaño de un auto transportan chasis o componentes clave como motores, suspensiones y baterías. Todas estas plataformas son autónomas, pueden girar sobre su eje, evitan obstáculos y regresan solas a sus bases de carga mediante conectividad Wi-Fi dedicada.
Una estación robótica instala los parabrisas, mientras que el ensamblaje final se realiza en plataformas adaptativas que se ajustan a la medida de cada vehículo. El sistema fue diseñado desde cero para permitir el ensamblaje de múltiples formatos sin necesidad de rediseñar procesos o interrumpir la producción.
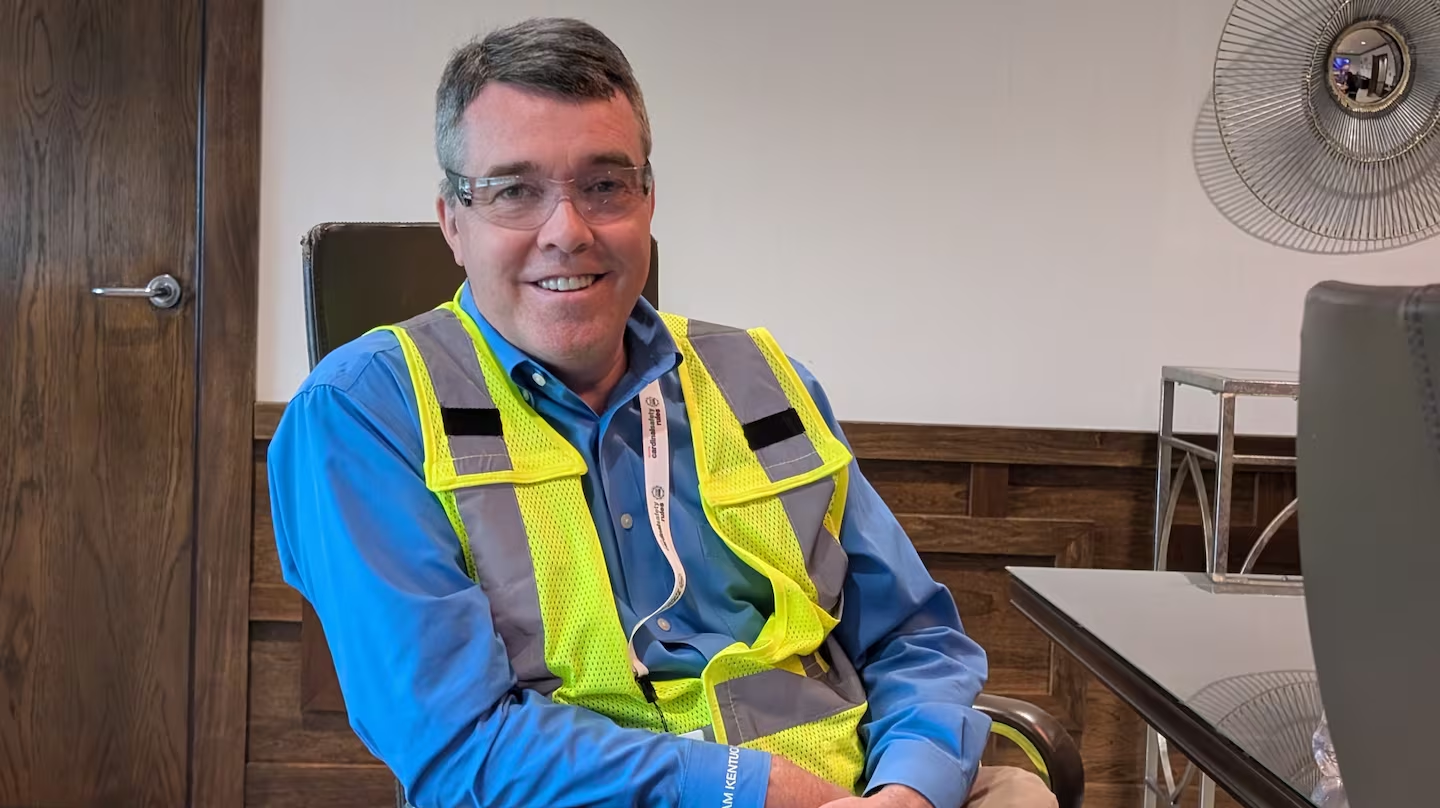
Una fábrica más limpia, eficiente y humana
Más allá de la flexibilidad técnica, la nueva Línea 1 también ha mejorado las condiciones laborales. El rediseño permitió abrir espacios, instalar grandes ventiladores, mejorar la iluminación y reducir el ruido, todo sin despedir empleados durante el proceso de transformación.
Toyota asegura que esta planta se convierte ahora en el nuevo estándar global para sus fábricas. Y no es solo por la tecnología: también representa una filosofía de producción basada en la adaptación continua, la eficiencia energética y la preparación para el futuro eléctrico.
“No gastamos todo este dinero para no usarlo”, afirma Brennan. “Hay planes para ponerla en funcionamiento con nuevos modelos. Créeme”.
Con la producción del Camry aún en curso, la Línea 1 se prepara para recibir vehículos eléctricos y enchufables de tres filas en los próximos meses, acercando cada vez más el concepto de producción “bajo demanda” al corazón de la manufactura moderna.